Injection Mold Design: A Comprehensive Guide
- Ankit Surkutwar
- Jul 4, 2023
- 2 min read
Introduction
Injection molding is a widely-used manufacturing process that enables the production of high-quality plastic parts in large volumes. One crucial aspect of this process is the design of the injection mold. In this blog post, we will explore the key considerations and steps involved in injection mold design.
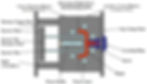
Understand the Requirements
Before diving into the mold design process, it is important to have a clear understanding of the requirements of the plastic part to be produced. This includes factors such as
Part dimensions
Tolerances
Material Properties
Production volume.
Mold Design Considerations
Designing an effective injection mold requires careful consideration of several factors. Here are some of the key aspects to focus on:
Parting Line: Determining the parting line is the first step in mold design. It determines how the mold will be split into two halves, allowing for easy removal of the part.
Gates and Runners: The location and design of gates and runners are crucial in ensuring proper material flow and filling of the mold cavity. Proper placement of these components reduces the chances of defects such as air traps, short shots, and sink marks.
Ejector System: An effective ejector system ensures easy removal of the part from the mold. It includes ejector pins, sliders, and lifters, which are strategically placed to avoid interference with the part geometry.
Cooling System: Efficient cooling is crucial for the overall cycle time and quality of the molded part. Proper placement of cooling channels facilitates uniform cooling and prevents warpage.
Venting: Adequate venting ensures the escape of air and gases from the mold cavity during the injection process. Insufficient venting can lead to defects such as burns, voids, or gas traps.
Mold Materials: The choice of mold materials depends on factors such as part volume, material properties, and production volume. Common materials used include steel alloys and aluminum alloys.
Mold Design Process
The mold design process typically involves the following steps:
Analyze Part Design: Understand the intricacies of the plastic part to be molded. Identify potential issues and design challenges.
Determine Mold Type: Choose between different mold types, such as two-plate mold, three-plate mold, or hot runner mold, based on the part design and requirements.
Create Mold Base: Design the mold base that acts as the foundation for the mold. It holds the various mold components together.
Design Cavity and Core: Develop the cavity and core inserts that form the actual shape of the part.
Incorporate Features: Add necessary features such as slides, lifters, and cooling channels to the mold design.
Finalize Mold Design: Review and revise the mold design, considering factors such as manufacturability, cost-effectiveness, and ease of maintenance.
Validate Mold Design: Conduct mold flow analysis and simulation to ensure optimal material flow and identify potential issues before production.
Conclusion
Injection mold design plays a crucial role in the success of the injection molding process. By understanding the requirements, considering key design aspects, and following a systematic design process, engineers can create molds that produce high-quality plastic parts efficiently and cost-effectively. Proper mold design not only ensures the smooth production of plastic parts but also contributes to the overall success of the manufacturing process.
I hope that this guide has provided you with valuable insights into injection mold designing. Stay tuned for more posts where we'll delve deeper into the world of manufacturing and explore other interesting topics. Happy learning!